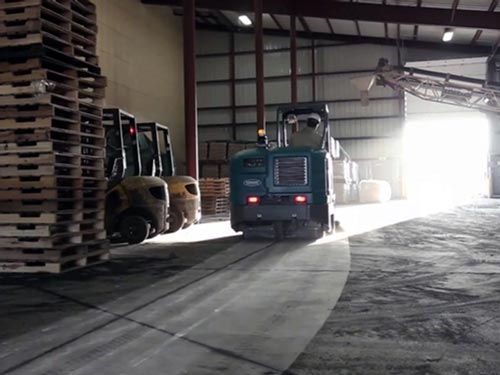
Grocery distribution centers accumulate a fair share of debris and, consequently, germs from the steady flow of food and foot traffic necessary for order fulfillment. In particular, the floors of these facilities require a significant amount of attention to combat the buildup of unsanitary dirt and litter. Commercial floor scrubbers work to maintain clean and safe facilities by picking up debris with vacuum suction technology and washing away dirt with industrial-grade squeegees for a spotless finish. Since you rely on your floor cleaning machines to keep your facility safe for the health of your employees, you understand the importance of a floor care routine that is mindful of regular maintenance.
Despite your best upkeep efforts, though, you might notice that your machine is underperforming. Fortunately for your wallet, buying a new machine is likely not the route you’ll have to go. An experienced floor scrubber service team will be able to help thanks to their expertise in machine parts and repair requirements. However, before you get on the phone, check out these five signs that indicate your floor scrubber or sweeper is in need of professional help.
Poor Suction
Poor floor scrubber suction can lead to water in unwanted places, including in pools on your facility’s floor and in the recovery tank of your machine. If your machine loses suction, listen to the vacuum motor for a grinding or high-pitched whine sound. This is a good indication that you need a new motor.
If you do not hear any atypical noises from your motor, there are several other reasons why your machine is not picking up water that would be best identified by a professional floor scrubber service technician. But first, try checking the following areas for potential blockages or leaks:
- In the recovery tank, check the float cage is debris-free and has one or, depending on the machine, both of its plastic balls within its cylindrical screen. A clogged float or dislodged ball can cause a blockage between the tank and the vacuum motor that prevents strong suction.
- Check the lid on your recovery tank is properly sealed. If the lid is easily removable when the motor is running, that means there is an air leak causing weak suction.
- Check the vacuum hose and, if applicable, the attached fitting for clogs or leaks. Remove the vacuum hose from the squeegee assembly and lower the squeegee deck. Then, click the bail to turn on the vacuum motor to test the suction power and check for subsequent blockages or pinholes. If there is a clog, it will need to be expertly flushed whereas a leak may necessitate a new hose entirely.
Reduced Run Time
Battery issues are the most common reasons you are not getting as much run time on your floor scrubber or sweeper as you did in the past. While more seasonal businesses allow floor scrubbers to remain idle for long periods of time, wholesale grocery distribution facilities require constant use of their commercial machines for often long stretches of time.
When your machine performs at maximum power or your motor has to work harder, the battery will drain quicker and, as a result, reduce runtime. Specifically, debris caught or wound around a scrubber’s brushes will limit mobility and force your machine to work overtime unnecessarily. Additionally, maintaining proper fluid levels in flooded lead-acid batteries is an essential component of floor scrubber battery maintenance with temperature, humidity, and age all conditions that result in more water usage.
Regardless of how frequently a scrubber is active in your distribution facility, regular battery checks and maintenance are a must in order to maximize the length of time your machine can operate. Trained floor scrubber service technicians will help you monitor and maintain proper water levels, check for loose or corroded connections, and ensure maximum battery life for peak productivity and cost-effective results.
Trouble Moving Forward or Reverse
Another sign that you should have your floor scrubber serviced is when the machine fails to move forward or backward. Possibly, this particular problem is a consequence of a broken part or mechanical or technical malfunction. Part replacement is a normal part of overall floor scrubber maintenance. Further, as machines become more sophisticated in design, there are more opportunities for one piece of hardware to fail.
On the other hand, if your industrial floor scrubber or sweeper is not moving, the battery may once again be the cause of the problem. The battery acts as a power source for every part of your machine. If one component draws too much power, another piece of your machine may suffer. Any type of operational issue is better prevented and resolved by an experienced service team.
Vacuum Motor Won’t Turn Off
It seems pretty bizarre, but a vacuum motor that refuses to turn off is an issue you might encounter. Sometimes, the vacuum motor stays engaged despite the squeegee assembly being raised. One solution is to reset the floor scrubber. Unfortunately, this is not a guaranteed resolution so you may want to have the phone number for a floor scrubber repair team at-the-ready.
Leaky Floor Scrubber
If your machine is leaking, it is time to schedule a service appointment. Whether from the hose, tank, or brush deck, it will not be long before you see other performance issues. Undesirable water can be detrimental to your machine’s operation and lead to safety concerns in your facility. Worse, the leaking water could be mixed with chemicals that are explicitly for cleaning purposes. As soon as you suspect a leak, contact a professional repair service.
As with any industrial machine, routine maintenance is the best way to get the most life out of your investment. At a busy 24/7 grocery distribution facility it can be difficult to keep up with and prioritize even basic scrubber and sweeper care. At Factory Cleaning Equipment, we offer flexible planned maintenance schedules with a flat fee tailored to your personal equipment needs. Our on-site maintenance services go above and beyond for facilities in Central Florida, Georgia, North and South Carolina, Illinois, Texas, and Colorado. For facilities in other areas of the country, we’ll connect you with experienced technicians from our partner service providers. We ensure your scrubber or sweeper is properly stored, charged, and operated to maximize its lifespan.
The floor scrubber maintenance and repair experts at Factory Cleaning Equipment are here to help! Whether you've got an emergency on your hands or you want to schedule routine maintenance, call today or send us a message online to schedule your planned maintenance.